Veronte¶
Unit name¶
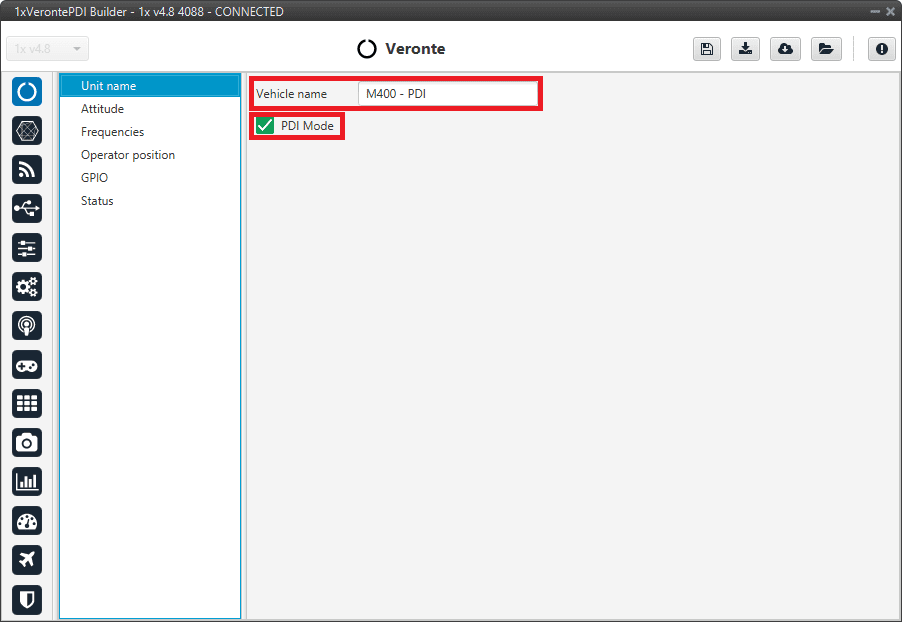
Unit name section¶
Vehicle name: The user can define the name of the configuration.
PDI Mode: It can be enabled or disabled. PDI mode allows the user to change the setup if 1x autopilot is not in INI phase.
Warning
Not being in PDI mode, the user cannot do out of the INI phase:
Reboot 1x autopilot
Change 1x setup (i.e. save to SD card)
Enter manually in maintenance mode
The variable ‘System error’ prevents operation in normal mode (not PDI mode). A list of all errors that can cause this bit to be set can be found in the Activation system error bits section of the 1x Software Manual.
If 1x autopilot has ‘sensors errors’ and is in normal mode (not PDI mode), the user will not be able to switch to another flight phase, it will remain in INI phase.
Tip
It is recommended to use normal mode when the configuration is finished, while PDI mode is useful during the development process.
Attitude¶
This menu allows the user to define the orientation of the autopilot with respect to the platform once it is installed. Aircraft axis are defined according to international aviation convention. 1x autopilot axis are drawn on the autopilot’s external case as defined in the Hardware Installation.
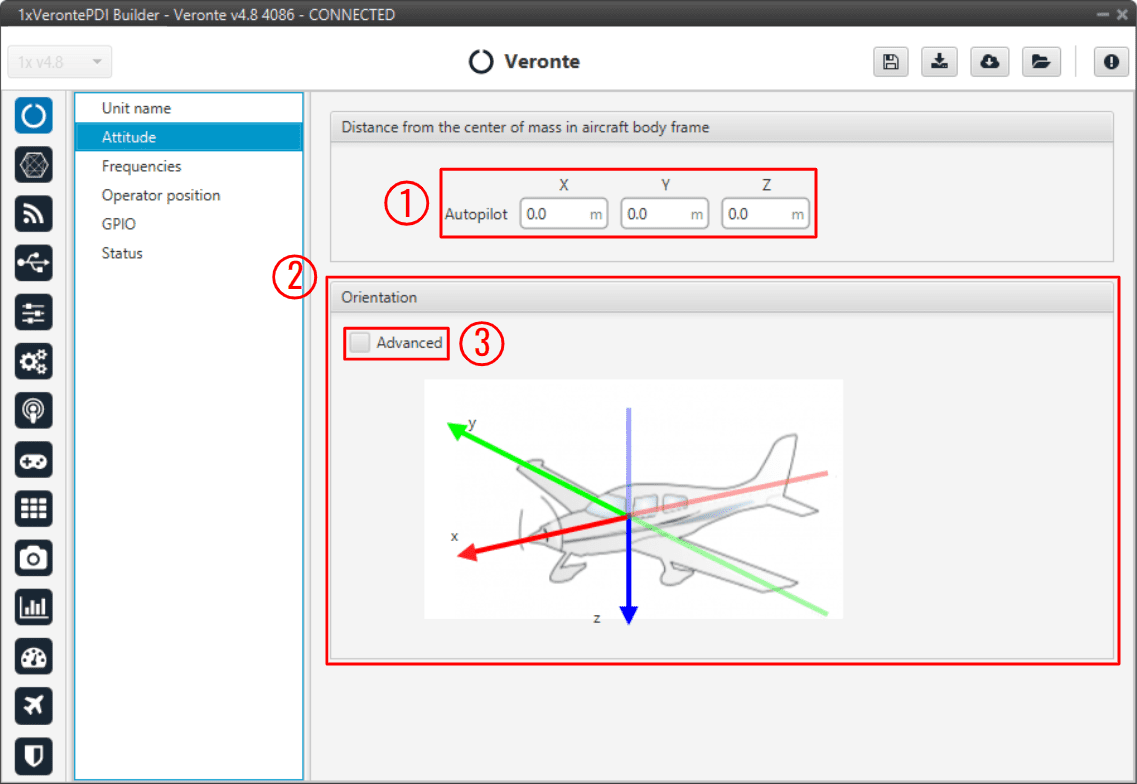
Attitude section¶
Distance from the center of mass in aircraft body frame: The autopilot’s distance from the centre of mass must be defined. This distance is entered in meters and accordingly to aircraft axis.
If the autopilot is not located in the centre of mass, it will measure a non-zero acceleration when turning. Distance from the center of mass in aircraft body frame will be used to compensate this value. An example is presented below:
Distance from the center of mass in aircraft body frame - Example¶
Distance from the center of mass in aircraft body frame - Example¶
Orientation: It is not compulsory to install the autopilot aligned with the aircraft axis. In order to indicate the autopilot’s relative position inside the platform, select the advanced option (3). A matrix relating vehicle axis and autopilot axis is needed to be filled in. The case of a non-orthogonal installation can be covered.
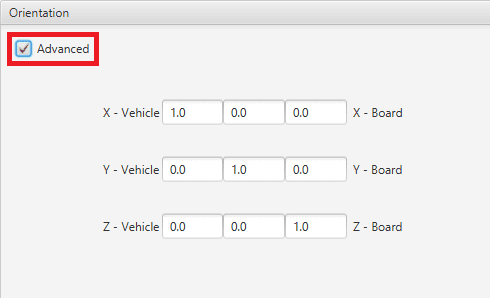
Advanced orientation¶
Note
If only a simple rotation is required, for example, a -90º rotation in the Z axis, it is simpler to select the correct axis directly in the ‘plane’:
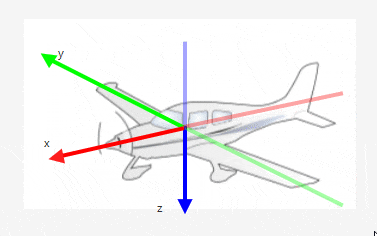
Change orientation¶
Frequencies¶
The frequency of the GNC task refers to the maximum working frequency of the core. In this case, 400 Hz, which is the maximum possible.
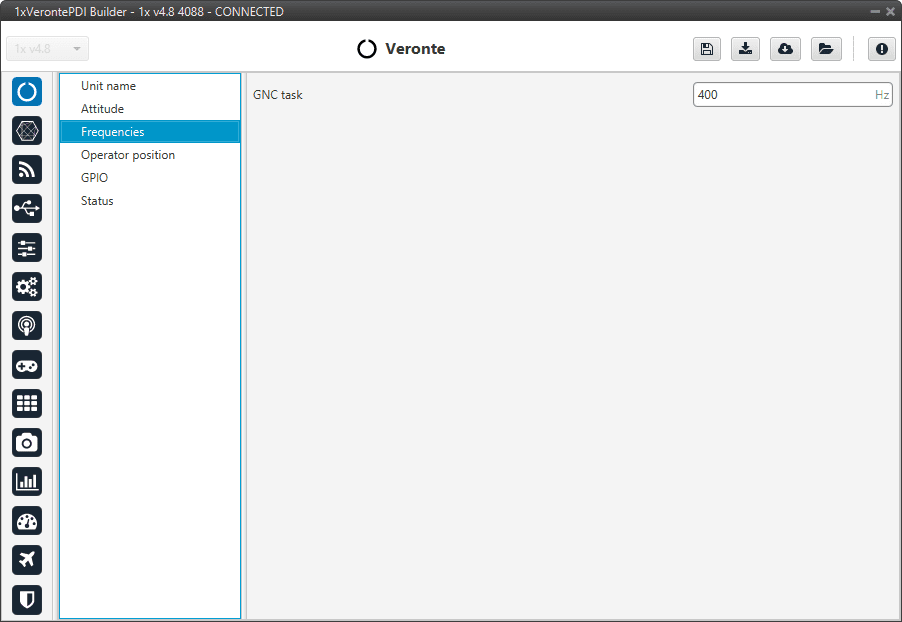
Frequencies section¶
Warning
Only 400 Hz can be used for simple configurations, so it is often necessary to reduce the frequency to 250-300 Hz. To find out why the user should reduce the GNC Task frequency, see Reduce GNC Task frequency -> Troubleshooting section of this manual.
Operator position¶
The operator position is the autopilot position from which the distance allowed by the licence is calculated.
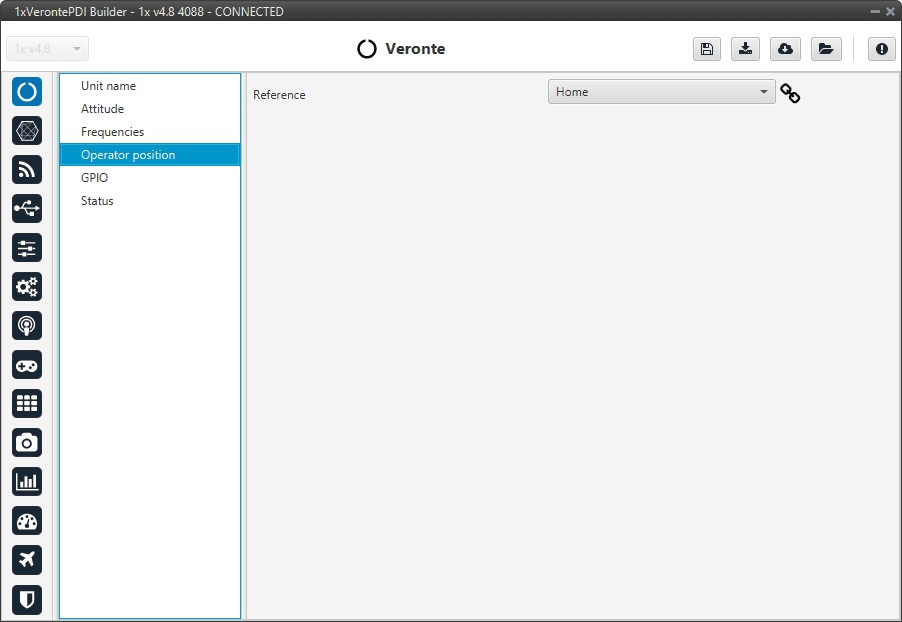
Operator position section¶
Tip
In operation, if the air unit does not have the license activated, it is recommended to set in the air unit the position of the ground unit.
GPIO¶
In this tab each individual GPIO behavior can be configured:
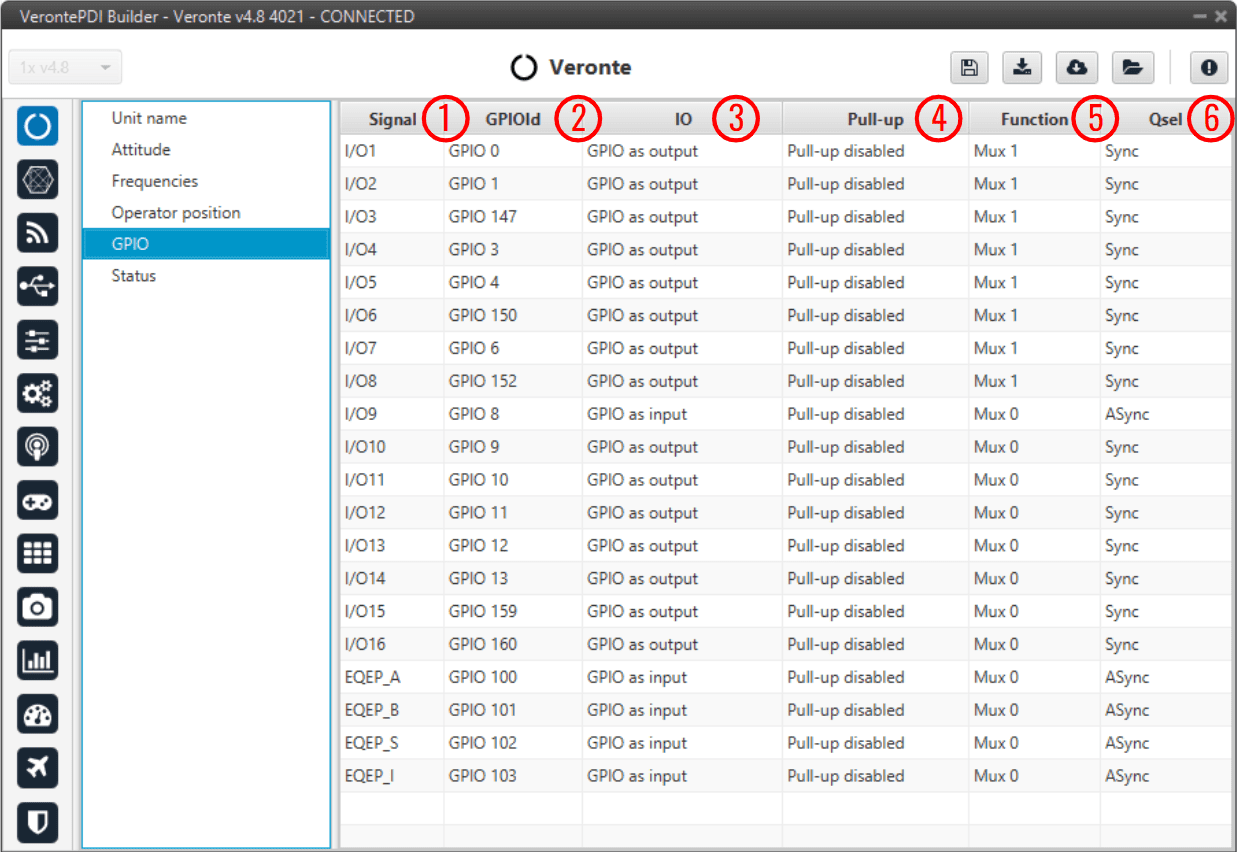
GPIO section¶
Signal: Pin ID as described in Hardware installation - Electrical section of the 1x user manual.
GPIOId: GPIO ID of the microcontroller.
IO: Define GPIO as an input or ouput.
Pull-up: Enable or disable the pull-up resistance.
Function: Mux 0: GPIO, Mux 1: PWM, Mux 2, Mux 3, etc. These are the different functionalities that the GPIO can have, this depends on the multiplexer.
Qsel: This is the “input qualification”, it is used to control how the value of a GPIO is evaluated. The available options are:
Sync: The value is taken as whatever is present at the time it is checked (synchronously). This is the default mode of all GPIO pins.
3 Samples: The value is checked 3 times and the value is only changed when the 3 times are the same.
6 Samples: Same as before, but checking 6 times instead of 3.
ASync: No checks are performed. It is used when it is not used as GPIO.
Status¶
This option enables the periodic sending of the status message that Veronte Link uses to recognise the 1x autopilot.
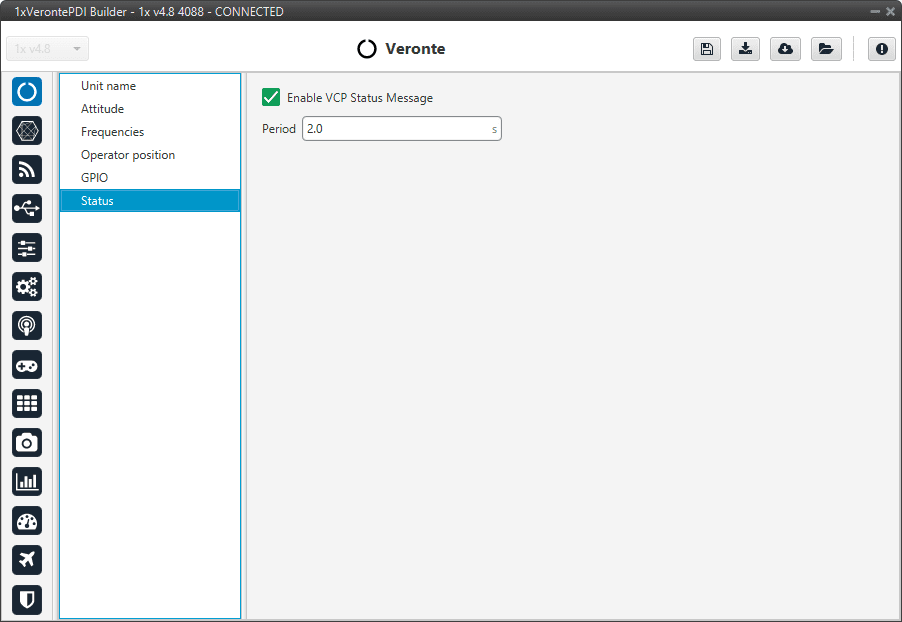
Status section¶
Period: Enter a desired period to send repeatedly the status message.
Note
VCP is the Veronte Communication Protocol. To know more, read the VCP user manual.